Ensuring Employee Safety: The Importance of Thorough Confined Space Risk Assessments
In various industries, employees often work in confined spaces that pose significant hazards. These spaces can be found in manufacturing plants, construction sites, and utilities. Ensuring the safety of employees working in confined spaces is imperative, and one way to achieve this is by conducting thorough confined space risk assessments.
This article will discuss the importance of these assessments, the key components involved, and how to effectively implement control measures to mitigate risks. A confined space risk assessment systematically evaluates the hazards and risks associated with working in confined spaces. This process helps employers identify potential dangers, implement appropriate control measures, and provide employees with the necessary training and equipment.
By conducting a comprehensive risk assessment, employers can ensure their workers’ safety and minimize the potential for accidents and incidents, ultimately promoting a safer work environment.
Defining confined spaces and their hazards
A confined space is large enough for a worker to enter and perform work but has limited access and exit points and is not designed for continuous occupancy. These spaces can be found in various forms, such as tanks, silos, tunnels, pits, and pipelines. The hazards associated with confined spaces can be grouped into three main categories: atmospheric risks, physical threats, and psychological hazards.
Atmospheric hazards include oxygen deficiency, toxic gases, and flammable or explosive atmospheres. Physical hazards involve risks such as engulfment, entrapment, falling objects, and mechanical hazards. Psychological threats stem from the potential for claustrophobia, stress, and anxiety due to the confined nature of the space. These hazards can result in serious injuries or fatalities if not adequately addressed and managed.
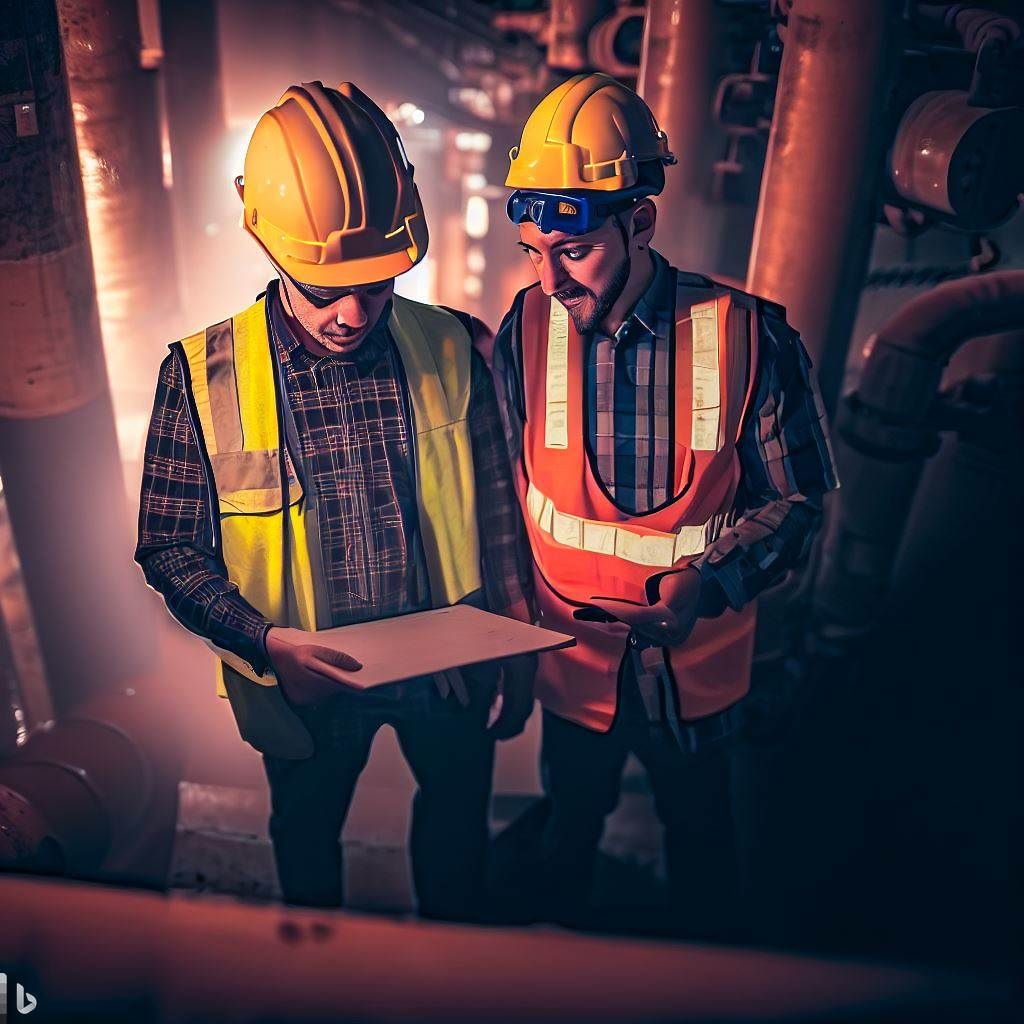
The importance of thorough confined space risk assessments
A confined space risk assessment is essential to ensure the safety of employees working in these environments. By conducting a comprehensive assessment, employers can identify potential hazards, evaluate their associated risks, and implement appropriate mitigation control measures. Additionally, risk assessments help employers determine the necessary training and equipment required for employees to work safely in confined spaces.
A thorough confined space risk assessment can also help prevent accidents and incidents, leading to costly downtime, legal repercussions, and damage to a company’s reputation. Moreover, conducting regular risk assessments demonstrates a commitment to employee safety, which can boost employee morale and productivity.
Key components of a confined space risk assessment
A confined space risk assessment should include the following key components:
- Identifying the confined spaces within the workplace
- Evaluating the potential hazards associated with each confined space
- Assessing the risks associated with the identified hazards
- Implementing control measures to mitigate the identified risks
- Providing training and equipment necessary for employees to work safely in confined spaces
- Appointing a competent person to oversee the risk assessment process
- Regularly reviewing and updating the risk assessment as needed
By addressing each of these components, employers can help ensure the safety of their employees working in confined spaces.
Identifying potential hazards in confined spaces
One of the first steps in conducting a confined space risk assessment is to identify the potential hazards within the confined space. This can be accomplished through observation, consultation with employees, and reviewing previous incident reports. Some common risks to consider include the following:
- Oxygen deficiency or enrichment
- Toxic gases or vapors
- Flammable or explosive atmospheres
- Engulfment or entrapment hazards
- Falling objects or materials
- Mechanical hazards, such as moving parts or machinery
- Slip, trip, and fall hazards
- Electric shock or electrocution
- Heat stress or cold stress
- Noise and vibration hazards
Once potential hazards have been identified, they should be documented and evaluated to determine the risk associated with each danger.
Implementing control measures to mitigate risks
After identifying and evaluating the potential hazards in a confined space, the next step is implementing control measures to mitigate the associated risks. Control measures should follow the hierarchy of controls, which prioritizes eliminating and substituting hazards, followed by engineering controls, administrative controls, and personal protective equipment (PPE).
Examples of control measures include:
- Eliminating the need to enter a confined space, such as by using remote monitoring systems or robotics
- Substituting hazardous materials or processes with safer alternatives
- Installing ventilation systems to improve air quality
- Implementing lockout/tagout procedures to prevent the accidental activation of machinery
- Establishing safe work procedures, such as entry and exit protocols
- Providing appropriate PPE, such as respiratory protection, fall protection, and protective clothing
Training and equipment for confined space work
Ensuring employees are properly trained and equipped is critical to confined space risk assessments. Training should be tailored to the specific hazards and risks associated with each confined space and cover topics such as hazard recognition, safe work procedures, and using PPE. In addition, employees should be trained in emergency response procedures, including evacuating a confined space and using rescue equipment.
The equipment required for confined space work will vary depending on the hazards and risks identified during the risk assessment. Some standard equipment used in confined spaces includes:
- Respiratory protection, such as air-purifying respirators or supplied-air respirators
- Fall protection equipment, such as harnesses, lanyards, and anchor points
- Gas detection and monitoring devices
- Ventilation equipment, such as fans or blowers
- Lighting, such as explosion-proof or intrinsically safe lights
- Communication devices, such as radios or intercom systems
- Rescue and retrieval equipment, such as tripod systems and winches
The role of a competent person in conducting confined space risk assessments
A competent person is an individual who has the necessary knowledge, skills, and experience to conduct confined space risk assessments and oversee the implementation of control measures. This person should be familiar with the hazards and risks associated with confined spaces in the workplace and the applicable regulations and standards governing confined space work.
A competent person plays a crucial role in ensuring the safety of employees working in confined spaces. They are responsible for conducting the risk assessment, implementing control measures, providing training and equipment, and regularly reviewing and updating the risk assessment as needed. Employers should ensure that a competent person is appointed and given the authority and resources to fulfill their role effectively.
Regular review and updating of confined space risk assessments
Confined space risk assessments should not be considered one-time event. Regular risk assessment inspection and updating are essential to remain current and relevant. Factors that may trigger a review of the risk assessment include:
- Changes to the confined space, such as modifications to its structure or function
- New hazards or risks that were not previously identified
- Changes to applicable regulations or standards
- Incidents or near misses involving the confined space
- Employee feedback or concerns
By regularly reviewing and updating the confined space risk assessment, employers can help ensure their employees continue working safely in these environments.
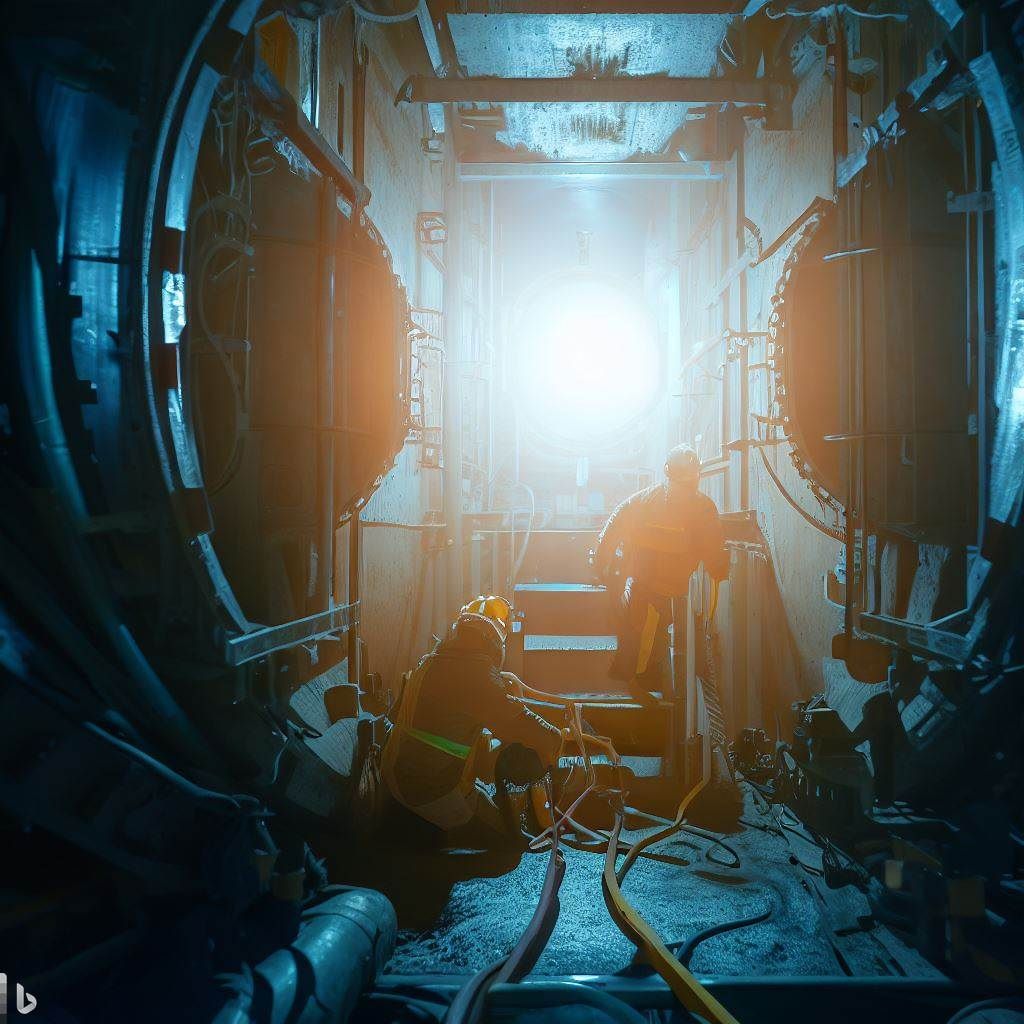
Conclusion: Prioritizing employee safety through effective risk assessments
Conducting thorough confined space risk assessments is crucial in ensuring the safety of employees working in confined spaces. By identifying potential hazards, evaluating the associated risks, and implementing appropriate control measures, employers can minimize the potential for accidents and incidents while promoting a safer work environment.
Furthermore, providing employees with the necessary training and equipment, and appointing a competent person to oversee the risk assessment process, demonstrates a commitment to employee safety that can foster a positive workplace culture.
Frequently Asked Questions:
What is a confined space risk assessment?
A confined space risk assessment is a systematic process of evaluating the hazards and risks associated with working in confined spaces to ensure the safety of employees.
Why is it important to conduct a confined space risk assessment?
Conducting a confined space risk assessment helps employers identify potential hazards, implement appropriate control measures, and provide the necessary training and equipment for employees to work safely in confined spaces. It can also help prevent accidents and incidents, leading to costly downtime, legal repercussions, and damage to a company’s reputation.
What are some common hazards associated with confined spaces?
Common risks in confined spaces include atmospheric hazards (oxygen deficiency, toxic gases, and flammable or explosive atmospheres), physical hazards (engulfment, entrapment, falling objects, and mechanical hazards), and psychological hazards (claustrophobia, stress, and anxiety due to the confined nature of the space).
What is the role of a competent person in confined space risk assessments?
A qualified person is responsible for conducting confined space risk assessments, implementing control measures, providing training and equipment, and regularly reviewing and updating the risk assessment as needed. They should have the necessary knowledge, skills, and experience to fulfill their role effectively.
How often should confine space risk assessments be reviewed and updated?
Confined space risk assessments should be reviewed and updated regularly to ensure their continued relevance and effectiveness. Factors that may trigger a review include changes to the confined space, new hazards or risks, changes to regulations or standards, incidents or near misses, and employee feedback or concerns.