Confined Space Definition According to OSHA
Navigating confined spaces in the workplace can be a serious challenge, and understanding OSHA’s definition of such environments is crucial for ensuring employee safety. This blog will dive into what constitutes a confined space according to OSHA guidelines, the hazards associated with these spaces, and measures to mitigate risks. We aim to arm you with essential knowledge that helps promote safe practices and adherence to regulatory standards in your industry.
Key Takeaways
- OSHA’s definition of a confined space includes criteria such as limited means of entry and exit, potential atmospheric hazards, and not being designed for continuous worker occupancy.
- Confined spaces can pose serious risks to workers, including atmospheric hazards such as oxygen-deficient or enriched atmospheres and physical hazards like engulfment, unguarded machinery, exposed live wires, heat stress, fire, and explosions.
- OSHA defines two types of confined spaces: permit-required (PRCS) and non-permit; PRCS require additional safety measures due to their hazardous characteristics, while non-permit still presents unique challenges requiring appropriate training for workers before entering.
- To ensure worker safety in confined spaces according to OSHA regulations, employers must conduct air monitoring regularly using calibrated equipment before allowing any authorized employee access to the space while providing appropriate personal protective equipment (PPE) like respirators, among others, based on risk factors associated with each environment involved along with effective emergency response plans tailored specifically towards either type (permit-required vs. non-permit).
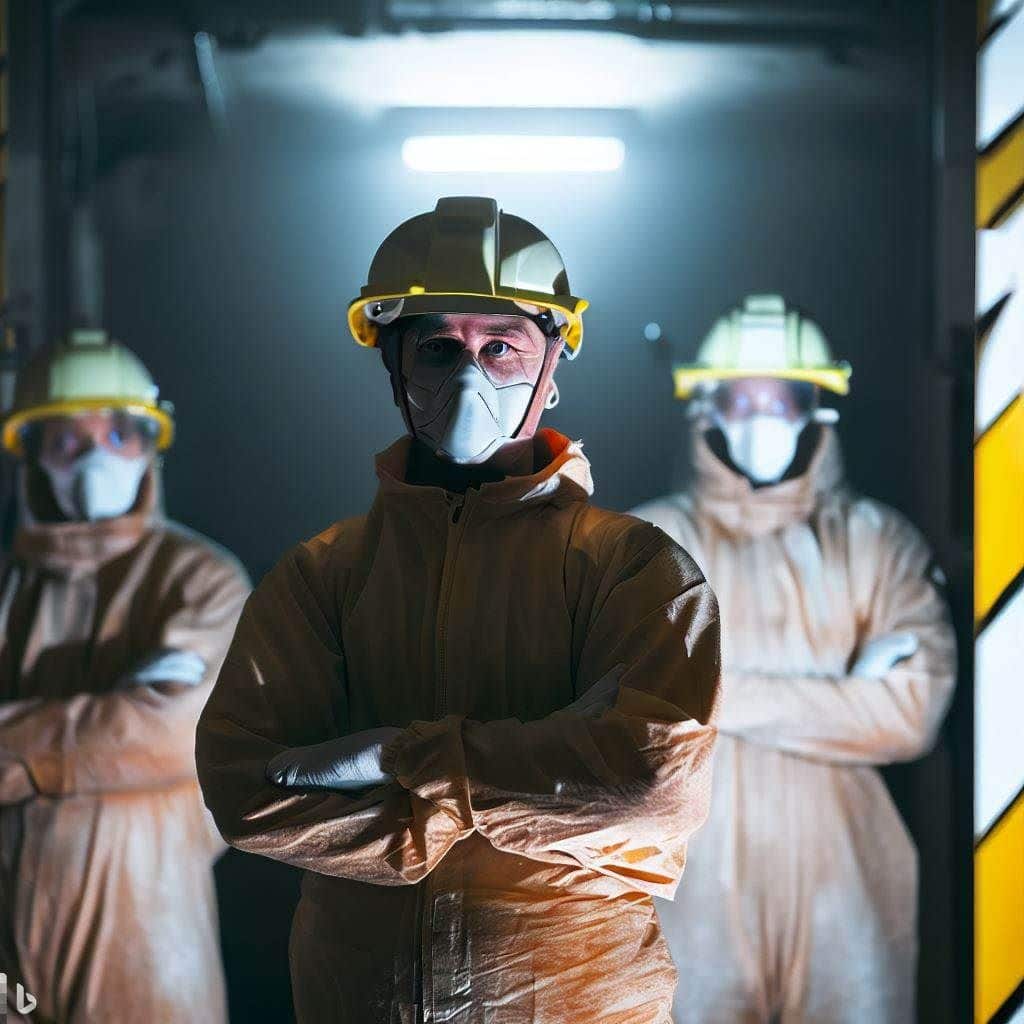
Understanding OSHA’s Definition Of A Confined Space
OSHA’s definition of a confined space includes specific criteria such as being large enough to enter and work in, having restricted means of entry or exit, and not being designed for continuous worker occupancy.
Criteria For The OSHA Confined Space Definition
To be considered a confined space under OSHA’s definition, a workspace must meet the following criteria:
- The space is large enough for an employee to enter and perform work.
- The space has limited or restricted means of entry and exit, making it difficult for workers to evacuate or be rescued quickly in an emergency.
- The space is not designed for continuous worker occupancy, which isn’t meant for long-term employee use.
- The space may contain potential atmospheric hazards, such as low oxygen levels, toxic gases, or combustible dust or vapors.
- The area could present physical hazards like engulfment, entrapment, loose materials that could shift or collapse, unguarded machinery, or exposed live wires.
Spaces meeting these criteria are subject to OSHA’s confined space regulations and require proper safety precautions and training to protect workers from potential hazards.
Examples Of Confined Spaces Per OSHA Definitions
Understanding the various examples of confined spaces according to OSHA definitions is crucial for maintaining worker safety. These include:
- Vaults
- Condenser Pits
- Fermenters
- Mash Tuns
- Silos
- Indoor Greenhouses
- Cultivation Rooms
- Grain Silos
- Keg Coolers (Cold Box)
- Manholes
- Pipe assemblies
- Ventilation Ducts
- Chemical/Water Tanks
- Sumps
- Containment Cavities
- Heat Sinks
- Electrical Transformers
These diverse types of confined spaces can pose serious risks, such as oxygen deficiency, hazardous atmospheres, and physical dangers like engulfment or unguarded machinery hazards, which makes it essential for workers to receive adequate training and follow OSHA guidelines before entering these areas to ensure their safety and well-being at work sites across various industries, including construction and agriculture sectors among others where permitted-required confined.
Space entry might be necessary as per 29 CFR 1910.146 standard enforced by the Occupational Safety and Health Administration in the United States Department of Labor regulations system for keeping workplaces safe from potential hazards related to insufficient air monitoring procedures or lack of proper equipment provision by employers as mandated under law provisions stipulated in comprehensive texts
outlining associated guidelines for better understanding specific requirements needed during operations conducted within enclosed settings where risks might arise based on unique circumstances impacting particular environments affected due to numerous factors that warrant consideration when determining risk levels involved for personnel
exposed accidentally or deliberately without prior preparation aimed at reducing incidence rates attributed mainly towards human errors resulting from negligence displayed occasionally amidst situations requiring attention immediately, often leading towards tragic consequences unfolding unexpectedly if preventative measures aren’t taken seriously beforehand when addressing inherent challenges linked directly with confined space conditions encountered routinely worldwide today.
Types Of Confined Spaces
OSHA defines two types of confined spaces: permit-required and non-permit, and understanding the differences between them is crucial for ensuring worker safety.
Permit-Required Confined Spaces
Permit-required confined spaces (PRCS) are defined by OSHA as those with hazardous characteristics, demanding strict regulations and safety measures for worker entry. These potentially dangerous areas require a written permit before any authorized employee can access the space.
Employers must implement adequate training programs and emergency response plans tailored to each PRCS to ensure worker safety in these high-risk environments. The area surrounding the entrance should be marked with warning signs indicating the presence of a permit-required confined space.
Additionally, OSHA mandates that companies designate trained attendants responsible for continually monitoring the workers inside these spaces while coordinating all necessary communication and rescue procedures if an incident occurs.
Non-Permit Confined Spaces
Non-permit confined spaces are areas that meet the definition of a confined space but do not have hazardous characteristics. These spaces still require precautions to ensure worker safety, such as testing breathable air quality, forced ventilation, and pre-determined rescue plans in case an accident occurs.
It’s important to note that even though these confined spaces aren’t considered permit-required by OSHA standards, they can still present unique challenges and dangers to workers.
Employers must provide proper training on how best to handle these situations safely. Accidents involving non-permit confined spaces can still be catastrophic if not handled properly.
Confined Space Hazards
Confined spaces present various hazards to workers, including atmospheric hazards such as oxygen-deficient or enriched atmospheres, physical hazards like engulfment and entanglement in moving parts, and energy and thermal hazards.
Atmospheric Hazards
Atmospheric hazards are a leading cause of danger in confined spaces, impacting air quality and presenting immediate health or life hazards. Here are some key facts:
- Oxygen concentration, toxic gases, and flammable material are three atmospheric conditions that must be monitored continuously while a space is occupied.
- Acceptable atmospheric conditions must be verified before entry and reverified to ensure ongoing safety.
- Harmful dust or gases can accumulate quickly in confined spaces, posing significant risks to workers’ respiratory health.
- Asphyxiation can occur due to low oxygen levels or dangerous gases such as carbon monoxide, methane, or hydrogen sulfide.
- Submersion in liquids or free-flowing granular solids can also occur in confined spaces, leading to serious injury or death from drowning or suffocation.
- Workers must have appropriate personal protective equipment (PPE), including respirators and full-body harnesses with retractable lifelines when working in confined spaces where atmospheric hazards may arise.
Physical Hazards
Physical hazards in confined spaces pose a significant risk to workers. These hazards can include:
- Engulfment: Workers can become engulfed by grain, sand, or water. This can happen quickly and without warning, making it difficult for other workers to rescue them.
- Unguarded machinery: Machinery that is not properly guarded or maintained can cause serious injuries or fatalities if workers come into contact with moving parts.
- Exposed live wires: Live wires in a confined space can electrocute workers if they contact them directly or indirectly.
- Heat stress: Working in hot temperatures without proper ventilation or cooling measures can lead to heat exhaustion, dehydration, and heat stroke.
- Fire and explosions: Confined spaces containing flammable materials or chemicals can ignite or explode if exposed to an ignition source.
To prevent physical hazards in confined spaces, employers must identify and evaluate the potential risks before allowing workers to enter. They must also provide proper training and equipment for workers inside the confined space, such as self-rescue devices and gas monitors. Additionally, employers must follow OSHA regulations for confined spaces and develop a written permit-required confined space program.
In conclusion, physical hazards are a serious concern for workers in confined spaces. Employers must take necessary steps to prevent these hazards and protect their employees from harm.
OSHA Confined Space Requirements
Employers must ensure air monitoring is conducted to determine acceptable entry conditions before and during entry and provide personal protective equipment and rescue services.
Air Monitoring Requirements
One critical requirement associated with OSHA confined space regulations is air monitoring. The atmosphere in a confined space can be hazardous due to toxic gases, flammable vapors, or reduced oxygen levels.
Air monitoring must be conducted before and during entry to ensure that acceptable conditions are maintained for workers’ safety. Monitoring equipment should be calibrated regularly to provide accurate readings.
Although gas detection monitors are crucial for sensing gas concentrations in dangerous spaces, they do not eliminate the need for proper ventilation and personal protective equipment (PPE).
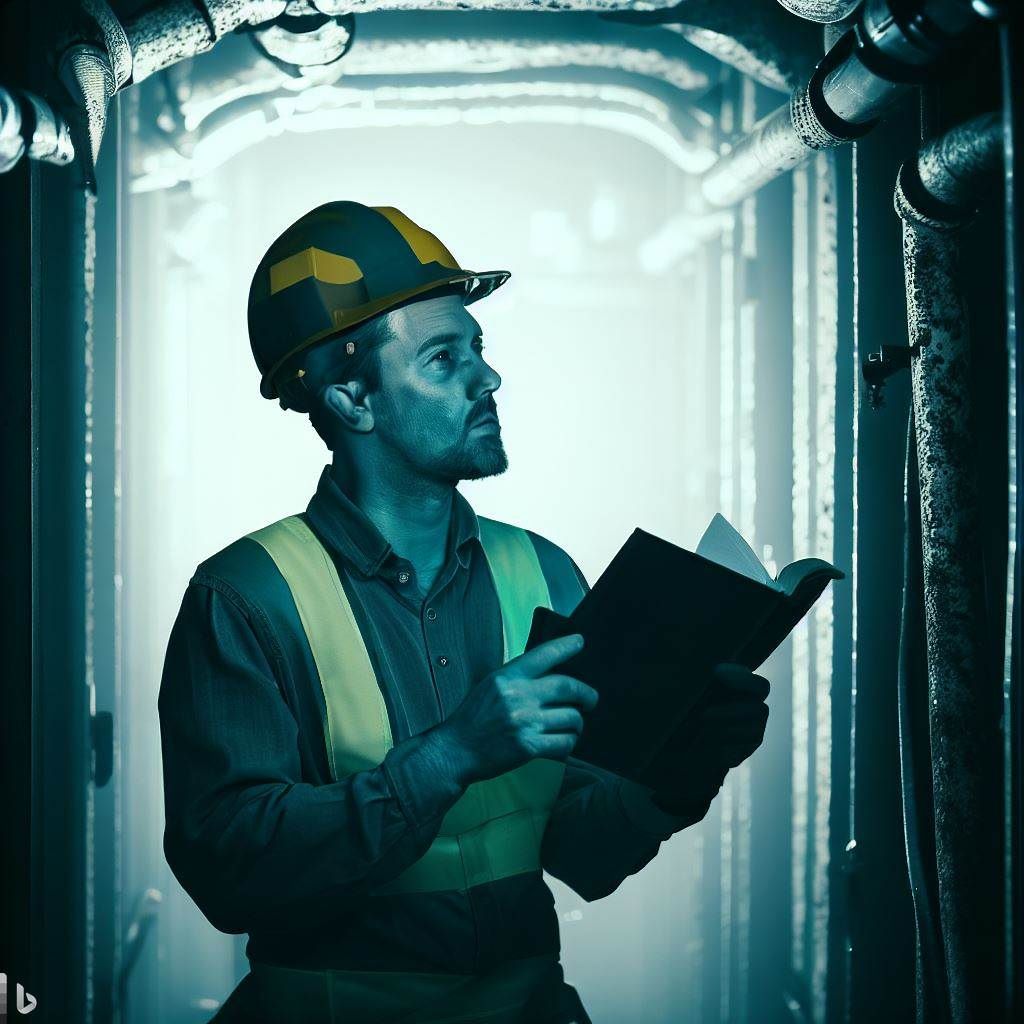
Confined Space Equipment And Monitoring
Proper confined space equipment and monitoring are crucial to ensure worker safety in confined spaces. This includes gas detection equipment, ventilating equipment, and warning signage.
Gas detection safety monitors can detect any hazardous gases in the atmosphere, while enclosed area safety monitors can alert workers when entering an unsafe area. Remote CO2 Storage Safety 3 Alarm or RAD-0002-ZR Oxygen Deficiency Alarm is important for continuously monitoring oxygen concentration levels.
Furthermore, employers must pay close attention to the air quality within a confined space before entry by testing it with proper atmospheric testing instruments like air sampling pumps with detector tubes or electronic sniffers for gas measurement.
Importance Of OSHA Confined Space Standards And Training
Ensuring that workers are protected from the hazards of confined spaces is critical to their safety and well-being. OSHA’s Confined Spaces standards require employers to identify, assess, and control hazards in confined spaces through a permit system.
OSHA also requires all employees who work in or around permit-required confined spaces to be trained on these requirements. Training should include identifying potential hazards within these spaces and appropriate emergency response procedures.
Failure to comply with these standards can result in severe consequences such as injuries or fatalities to workers, citations for non-compliance with OSHA regulations, and legal action against the employer under federal laws requiring safer workplace conditions.
As an example of why training is essential: between 2011-2018, there were over 1k occupational injuries related to working inside confined spaces causing serious injury or even death – this highlights how important it is for workers and companies alike to need quality training programs which are regularly updated with new information regarding hazardous gases/procedures on site!
Conclusion
In conclusion, understanding OSHA’s confined space definition is crucial for maintaining workplace safety and complying with regulatory standards. Employers can prevent accidents, injuries, and fatalities by identifying potential hazards and implementing appropriate measures to protect employees working in confined spaces. Whether through air monitoring requirements or specialized equipment like gas detection monitors, employers must proactively ensure their workers’ well-being.
Frequently Asked Questions:
1. What is OSHA’s definition of a confined space in the workplace?
According to OSHA, a confined space is an area that meets three criteria: it must be large enough for an employee to enter and perform work; it has limited or restricted means of entry or exit; and it is not designed for continuous occupancy.
2. What are some examples of confined spaces in the workplace?
Examples of confined spaces include manholes, crawl spaces, tanks, pipes, boilers, ducts, and other areas with limited access points.
3. Why does OSHA require employers to have specific procedures for working in confined spaces?
OSHA requires specific procedures for working in confined spaces because they pose hazards such as asphyxiation due to lack of oxygen or exposure to hazardous chemicals that can be deadly if not properly addressed before entry.
4. What steps should employers take to ensure safety while working in a confined space?
Employers should conduct a thorough risk assessment before allowing employees into a potentially dangerous area, including testing the atmosphere. Employees must also be trained on proper precautions & how to keep themselves safe while inside, including using personal protective equipment (PPE), having emergency rescue plans prepared, using ventilation systems when necessary & ensuring tools are secured during transport. Hence, no one trips over them accidentally upon exiting the work zone.