Understanding Confined Space Gas Limits: OSHA Guidelines and Best Practices for Workplace Safety
Working in confined spaces presents unique challenges and risks, particularly regarding gas exposure. Understanding the limits and regulations surrounding gas exposure in confined spaces is essential to ensuring the safety of workers and maintaining regulatory compliance. This article will provide an in-depth look at confined space gas limits, the Occupational Safety and Health Administration’s (OSHA) guidelines, and best practices for maintaining workplace safety.
Confined space gas limits are critical to workplace safety, as they help prevent hazardous gas exposure, which can lead to severe injury or even death. By thoroughly understanding these limits and the necessary precautions, employers and employees can work together to create a safe and healthy work environment.
This comprehensive guide will cover the definition of confined spaces according to OSHA, their guidelines for gas limits, common hazardous gases found in confined spaces, the importance of gas monitoring, best practices for safety, personal protective equipment, training and certification, and developing a confined space safety program.
What is a confined space, according to OSHA?
According to OSHA, a confined space is an area that is large enough for a worker to enter and perform work but has limited means of entry and exit and is not designed for continuous occupancy. These spaces can include tanks, silos, tunnels, pipelines, and pits. Confined spaces can present serious hazards, including toxic gas exposure, oxygen deficiency, and the risk of fire or explosion.
OSHA has specific regulations in place to protect workers in these environments. These regulations, found under the Permit-Required Confined Spaces Standard (29 CFR 1910.146), outline the requirements for employers to identify confined spaces, evaluate their hazards, and implement necessary safety measures.
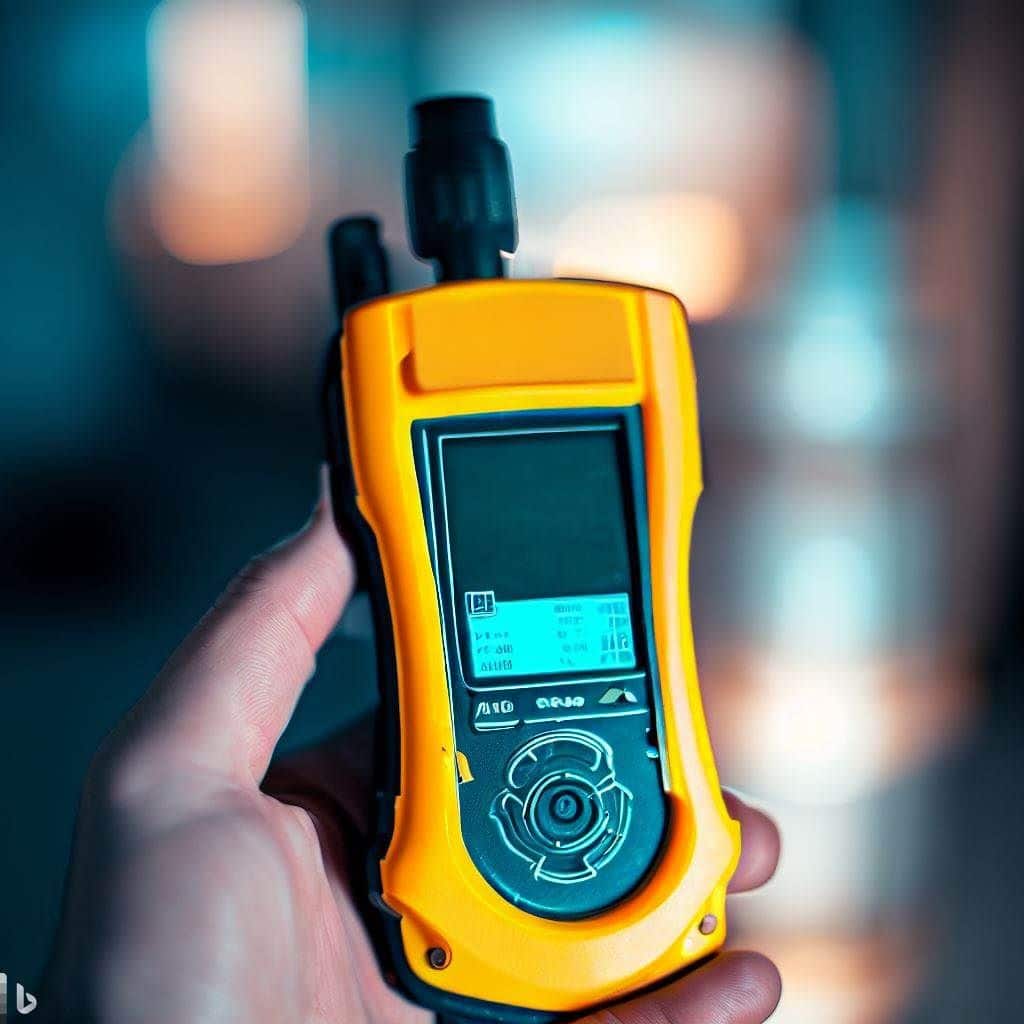
OSHA guidelines for confined space gas limits
The OSHA guidelines for confined space gas limits are in place to protect workers from hazardous gas exposure. These limits are determined by the Permissible Exposure Limits (PELs), which are the maximum allowable concentrations of hazardous substances in the workplace. PELs are established for various gases, including oxygen, carbon monoxide, hydrogen sulfide, and other toxic gases.
For confined spaces, OSHA requires the following gas limits:
- Oxygen: The oxygen concentration must be maintained between 19.5% and 23.5%. Levels below 19.5% are considered oxygen-deficient, while levels above 23.5% pose an increased risk of fire or explosion.
- Carbon monoxide: The PEL for carbon monoxide is 50 parts per million (ppm) over an 8-hour time-weighted average.
- Hydrogen sulfide: The PEL for hydrogen sulfide is 20 ppm over an 8-hour time-weighted average, with a ceiling limit of 50 ppm that must not be exceeded at any time.
- Other toxic gases: For other hazardous gases, OSHA has established specific PELs that must be adhered to in confined spaces.
Employers are responsible for monitoring and maintaining gas levels within these limits to ensure worker safety.
Common hazardous gases found in confined spaces
Various hazardous gases can be found in confined spaces, depending on the work’s nature and materials. Some of the most common dangerous gases include:
- Oxygen deficiency occurs when the oxygen level in the confined space falls below 19.5% and can lead to asphyxiation, impaired judgment, and unconsciousness.
- Carbon monoxide: This colorless, odorless, and tasteless gas is produced by incomplete combustion of organic materials and can cause headaches, dizziness, nausea, and even death at high concentrations.
- Hydrogen sulfide: This toxic gas has a distinct rotten egg smell and is produced by the breakdown of organic materials without oxygen. Exposure to high levels can cause irritation, dizziness, unconsciousness, and death.
- Methane: This flammable and explosive gas is produced by decomposing organic materials and can displace oxygen, leading to asphyxiation.
- Volatile organic compounds (VOCs): These compounds can be found in solvents, paints, and other chemicals and can cause irritation, dizziness, and other health issues.
Understanding the specific hazards present in a confined space is essential for implementing appropriate safety measures and monitoring gas levels effectively.
The importance of gas monitoring in confined spaces
Gas monitoring is critical to confined space safety, as it helps ensure that gas levels remain within acceptable limits and alerts workers to potential hazards. Monitoring should be conducted before entry and continue throughout work in the confined space. There are several methods for gas monitoring, including direct reading instruments such as portable gas detectors, which can measure multiple gases simultaneously and provide real-time readings.
Another technique uses colorimetric tubes, which change color when exposed to specific gases and visually indicate concentration levels. By implementing effective gas monitoring practices, employers can quickly identify hazardous conditions and take appropriate action to protect their workers.
Best practices for confined space safety
To maintain a safe working environment in confined spaces, employers should adhere to the following best practices:
- Identify and evaluate confined spaces: Employers must determine if a space is confined and its potential hazards.
- Develop and implement a confined space safety program: This program should outline procedures for safe entry, work, and exit, as well as emergency response plans and training requirements.
- Train workers: All workers involved in confined space work should receive appropriate training in hazard identification, safe work practices, and emergency procedures.
- Use proper ventilation: Adequate ventilation can help maintain safe oxygen levels and dilute hazardous gases.
- Monitor gas levels: Continuous monitoring is crucial for identifying potential hazards and ensuring worker safety.
- Establish communication protocols: Effective communication between workers inside and outside the confined space is essential for maintaining safety and responding to emergencies.
- Use appropriate personal protective equipment (PPE): PPE, such as respirators, gloves, and protective clothing, can help protect workers from hazardous gas exposure and other risks.
Personal protective equipment (PPE) for confined space work
PPE is essential to confined space safety, as it helps protect workers from hazardous gas exposure and other risks. The type and level of PPE required will depend on the specific hazards present in the confined space. Some common types of PPE used in confined spaces include:
- Respiratory protection: Respirators, such as air-purifying or self-contained breathing apparatuses, can help protect workers from hazardous gas exposure.
- Eye and face protection: Safety goggles, face shields, and full-face respirators can protect you from chemical splashes, flying debris, and other hazards.
- Protective clothing: Coveralls, chemical-resistant suits, and other protective garments can help shield workers from contact with hazardous substances.
- Gloves: Chemical-resistant gloves can protect workers from exposure to hazardous materials.
- Fall protection: Harnesses, lanyards, and other fall protection equipment can help prevent falls and injuries in confined spaces.
Employers should ensure that workers are properly trained in using and maintaining PPE and that equipment is regularly inspected for damage or wear.
Training and certification for confined space safety
Training is critical to confined space safety, ensuring workers understand the hazards and precautions associated with their work. OSHA requires that all workers involved in confined space work receive appropriate training in hazard identification, safe work practices, and emergency procedures.
In addition to general confined space training, some workers may require specialized training or certification. For example, workers responsible for gas monitoring may need specific training on using and maintaining gas detection equipment.
Similarly, workers who perform rescue operations in confined spaces may require specialized rescue training and certification. Employers should ensure that all workers receive appropriate training and maintain their credentials as needed.
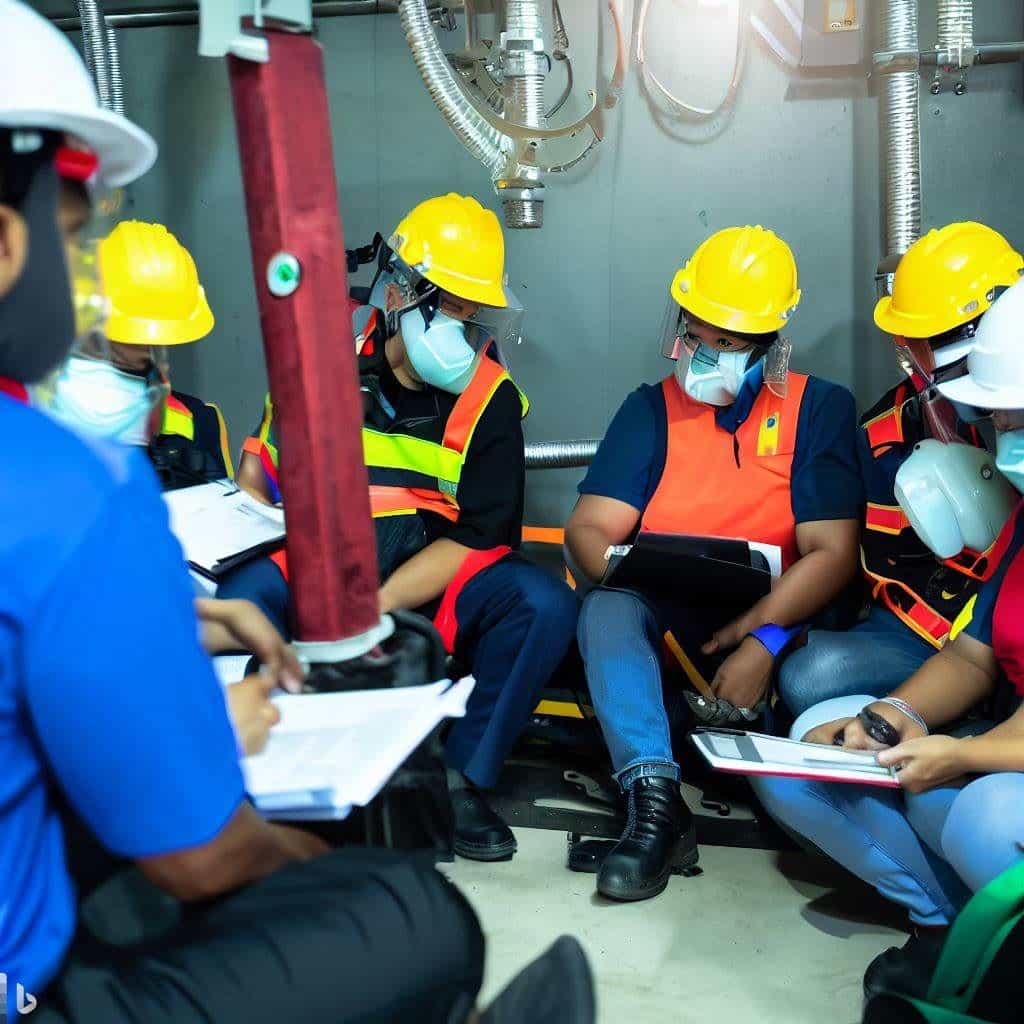
Developing a confined space safety program
A comprehensive confined space safety program is essential for maintaining a safe work environment and regulatory compliance. Employers should consider the following steps when developing their program:
- Identify and evaluate confined spaces: Determine if spaces are confined spaces and evaluate their potential hazards.
- Establish procedures for safe entry, work, and exit: Develop specific procedures for each confined space, including permit requirements, ventilation, and isolation of hazards.
- Implement gas monitoring practices: Establish gas monitoring protocols, including using appropriate equipment and continuous monitoring during work.
- Develop emergency response plans: Create emergency plans, including evacuation procedures and rescue operations.
- Train workers: Ensure that all workers receive appropriate training and maintain their certifications as required.
- Conduct regular inspections and audits: Inspect confined spaces, equipment, and working practices to identify potential hazards and ensure compliance with safety procedures.
- Continuously improve the program: Review and update the confined space safety program to address changing conditions and incorporate lessons learned from incidents or near-misses.
Conclusion and additional resources
Understanding confined space gas limits and following OSHA guidelines is essential for maintaining workplace safety and preventing hazardous gas exposure. By implementing best practices, using appropriate personal protective equipment, and providing proper training, employers can help protect their workers and maintain a safe and healthy work environment.
For additional information and resources on confined space safety, consider the following sources:
- OSHA’s Confined Spaces webpage: https://www.osha.gov/confined-spaces
- National Institute for Occupational Safety and Health (NIOSH) Confined Spaces topic page: https://www.cdc.gov/niosh/topics/confinedspace/
Frequently Asked Questions:
What is a confined space, according to OSHA?
A confined space is an area that is large enough for a worker to enter and perform work but has limited means of entry and exit and is not designed for continuous occupancy.
What are the OSHA guidelines for confined space gas limits?
OSHA guidelines for confined space gas limits are determined by Permissible Exposure Limits (PELs), the maximum allowable concentrations of hazardous substances in the workplace.
What are some common hazardous gases found in confined spaces?
Common hazardous gases in confined spaces include oxygen deficiency, carbon monoxide, hydrogen sulfide, methane, and volatile organic compounds (VOCs).
What is the importance of gas monitoring in confined spaces?
Gas monitoring is essential for ensuring that gas levels remain within acceptable limits and alerting workers to potential hazards.
What are some best practices for confined space safety?
Best practices for confined space safety include identifying and evaluating confined spaces, developing a confined space safety program, training workers, using proper ventilation, monitoring gas levels, establishing communication protocols, and using appropriate personal protective equipment (PPE).