Mastering OSHA Confined Space Air Monitoring Requirements: A Comprehensive Guide for Workplace Safety
As an experienced safety professional, I have witnessed firsthand the importance of understanding and adhering to the Occupational Safety and Health Administration (OSHA) confined space regulations. In this comprehensive guide, I will share my knowledge and experience to help you master the OSHA confined space air monitoring requirements and ensure workplace safety.
OSHA’s confined space regulations protect workers from the hazards of working in confined spaces. These regulations apply to general industry and construction and are covered under OSHA standards 29 CFR 1910.146 and 29 CFR 1926 Subpart AA, respectively. By understanding these regulations and implementing the required safety measures, employers can significantly reduce the risk of accidents, injuries, and fatalities in confined spaces.
In the following sections, we will discuss the key aspects of OSHA confined space air monitoring requirements, including understanding confined spaces and their hazards, identifying and classifying confined spaces, the role of air monitoring in confined space safety, and the necessary equipment and training for air monitoring personnel. By the end of this guide, you will have a solid foundation to develop and implement a confined space safety program that complies with OSHA regulations.
Understanding confined spaces and their hazards
OSHA defines confined spaces as spaces that have the following characteristics:
- Are large enough for a worker to enter and perform work;
- Have limited or restricted means of entry or exit;
- Are not designed for continuous occupancy.
Common examples of confined spaces include tanks, silos, vaults, pits, and tunnels. These spaces can be found in various industries, such as manufacturing, construction, and agriculture.
Working in confined spaces presents a unique set of hazards that can lead to serious injuries or fatalities if not properly addressed. Some of the most common hazards associated with confined spaces include:
- Oxygen deficiency or enrichment: Confined spaces can have an insufficient or excessively high concentration of oxygen, which can lead to asphyxiation or create a flammable atmosphere, respectively.
- Hazardous atmospheres: The presence of toxic or flammable gases, vapors, or dust can pose a risk of fire, explosion, or acute or chronic health effects for workers.
- Engulfment: Workers can become trapped or engulfed by loose materials, such as sand, grain, or liquids, resulting in suffocation or drowning.
- Entrapment: The configuration of a confined space can cause workers to become trapped or caught between objects, leading to injury or death.
- Physical hazards: Confined spaces can present risks such as extreme temperatures, noise, or hazardous substances or materials.
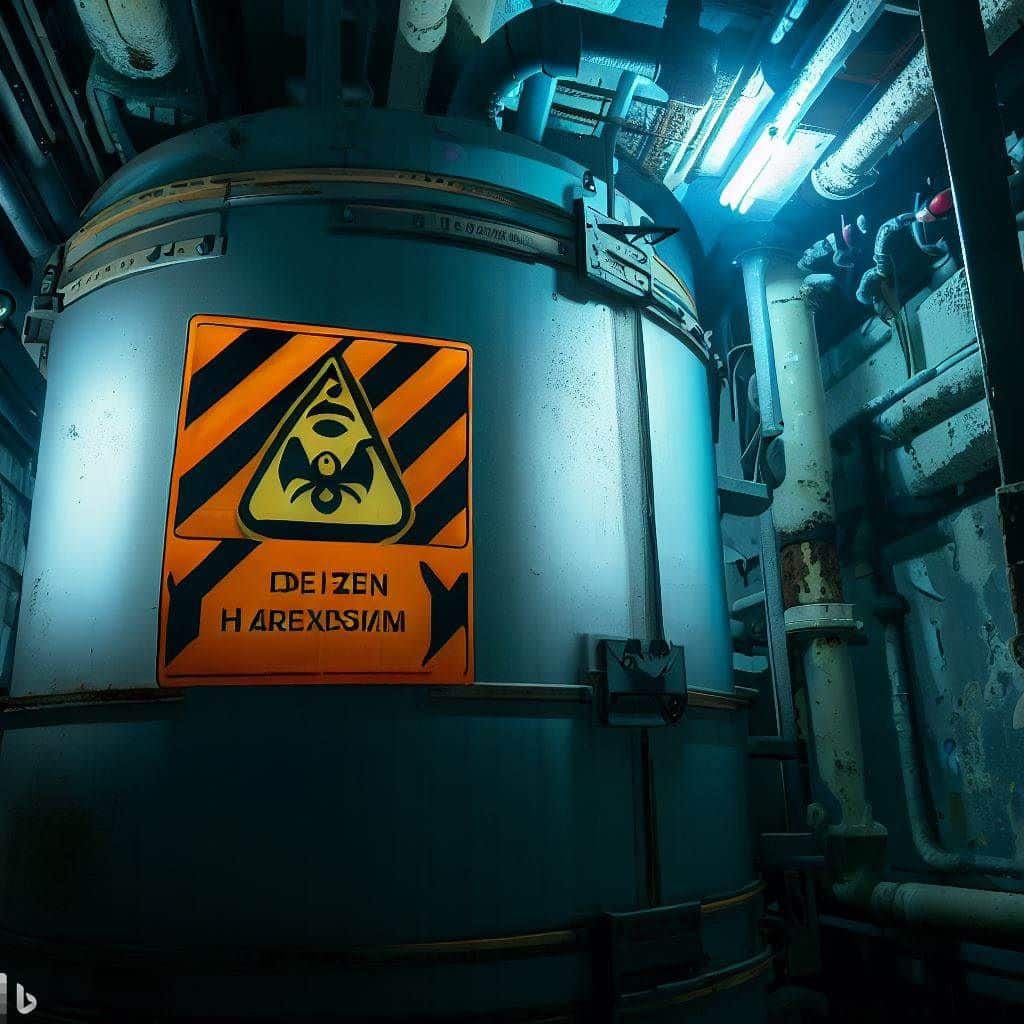
Key components of OSHA confined space air monitoring requirements
OSHA confined space air monitoring requirements are critical to confined space safety, as they help identify and mitigate the risks associated with hazardous atmospheres. The key components of these requirements include:
- Pre-entry testing: Employers must test the atmosphere within a confined space before workers enter to determine if it is safe for entry. This involves testing for oxygen levels, flammable gases and vapors, and potential toxic air contaminants. If the pre-entry testing reveals that the atmosphere is unsafe, the space must be ventilated, isolated, or otherwise made safe before entry.
- Continuous monitoring: Once a confined space has been deemed safe for entry, continuous monitoring of the atmosphere must ensure that conditions remain safe for workers. Monitoring must be conducted for oxygen levels, flammable gases and vapors, and potential toxic air contaminants.
- Alarm systems and procedures: Monitoring equipment must be equipped with alarm systems that alert workers when atmospheric conditions become unsafe. Employers must establish procedures for workers to follow in the event of an alarm, including evacuation and emergency response procedures.
- Documentation: Employers must maintain records of all confined space air monitoring activities, including pre-entry testing, continuous monitoring results, and any incidents or corrective actions taken.
By adhering to these requirements, employers can help to ensure that workers are protected from hazardous atmospheres and that confined spaces remain safe for entry and occupancy.
Identifying and classifying confined spaces
To effectively implement OSHA confined space air monitoring requirements, it is essential first to identify and classify the confined spaces within your workplace. OSHA defines two types of confined spaces: non-permit-required confined spaces and permit-required confined spaces.
Non-permit-required confined spaces are spaces that meet the definition of a confined space but do not contain or have the potential to contain any of the following hazards:
- Hazardous atmosphere
- Engulfment hazard
- Entrapment hazard
- Any other recognized serious safety or health hazard
Permit-required confined spaces meet the definition of a confined space and contain or have the potential to contain one or more of the hazards listed above. These spaces require a permit for entry, and employers must implement a permit-required confined space program to ensure the safety of workers.
To identify and classify confined spaces in your workplace, it is essential to conduct a thorough assessment of your facility, taking note of any spaces that meet the criteria for a confined space. Once these spaces have been identified, they should be evaluated for potential hazards to determine if they are non-permit-required or permit-required confined spaces.
The role of air monitoring in confined space safety
Air monitoring plays a crucial role in ensuring the safety of workers in confined spaces by identifying hazardous atmospheres and alerting workers to potential dangers. The primary objectives of air monitoring in confined space safety include:
- Assessing air quality for safe entry: By conducting pre-entry testing, employers can determine if the atmosphere within a confined space is safe for workers to enter. This helps to prevent workers from being exposed to hazardous atmospheres that could result in injury or death.
- Detecting changes in atmospheric conditions: Continuous air monitoring allows for the detection of changes in atmospheric conditions within a confined space, such as the introduction of toxic gases or a decrease in oxygen levels. By identifying these changes, workers can be alerted to potential hazards and take appropriate action to ensure their safety.
- Informing appropriate safety measures: The results of air monitoring can be used to inform the implementation of appropriate safety measures, such as ventilation, isolation, or the use of personal protective equipment (PPE). Employers can better protect workers from harm by tailoring safety measures to the specific hazards in a confined space.
Employers can significantly reduce the risk of accidents and injuries associated with hazardous atmospheres by understanding the importance of air monitoring in confined space safety and implementing the necessary procedures and equipment.
Equipment and tools used for air monitoring
To effectively conduct air monitoring in confined spaces, it is essential to have the appropriate equipment and tools. Some of the most commonly used equipment for confined space air monitoring include:
- Gas detectors: Portable gas detectors are used to measure the concentration of specific gases, such as oxygen, carbon monoxide, or hydrogen sulfide, in the atmosphere of a confined space. These devices typically use electrochemical sensors or infrared technology to detect the presence of gases and provide real-time readings.
- Combustible gas indicators: These devices are used to measure the concentration of flammable gases or vapors in the atmosphere of a confined space. Combustible gas indicators often use a catalytic bead or infrared technology to detect the presence of flammable substances and provide a percentage of the lower explosive limit (LEL) reading.
- Air sampling pumps and tubes: Air sampling pumps draw a sample of air from a confined space through a colorimetric detector tube, which changes color in the presence of a specific gas or vapor. The concentration of the gas or vapor can be determined by comparing the color change to a calibrated scale.
- Multi-gas monitors: Multi-gas monitors are portable devices that can detect and measure multiple gases simultaneously, such as oxygen, carbon monoxide, hydrogen sulfide, and combustible gases. These devices often use a combination of sensor technologies, such as electrochemical, catalytic bead, and infrared, to provide accurate and reliable measurements.
When selecting air monitoring equipment for your confined space safety program, it is important to consider factors such as the specific gases and hazards present in your workplace, the accuracy and reliability of the devices, and any calibration and maintenance requirements.
Training requirements for confined space air monitoring personnel
Proper training is essential for personnel responsible for conducting confined space air monitoring to ensure that they are competent in the use of monitoring equipment and can accurately interpret and respond to the results. OSHA confined space regulations require that employers provide training for personnel involved in confined space entry and rescue, including training on air monitoring procedures and equipment.
Training should cover the following topics:
- The hazards associated with confined spaces and hazardous atmospheres
- The principles of air monitoring, including the purpose and objectives of monitoring and the types of equipment used
- Proper use, calibration, and maintenance of air monitoring equipment
- The interpretation of air monitoring results, including understanding alarm levels and the actions required in response to alarms
- The proper documentation of air monitoring activities and results
In addition to initial training, employers should provide periodic refresher training to ensure that personnel remains competent and up-to-date on the latest best practices and technologies in confined space air monitoring.
Developing and implementing a confined space safety program
Employers should develop and implement a comprehensive confined space safety program to effectively manage the risks associated with confined spaces and ensure compliance with OSHA confined space air monitoring requirements. Key elements of a confined space safety program include:
- Identifying and classifying confined spaces in the workplace
- Developing and implementing procedures for pre-entry testing and continuous air monitoring
- Establishing procedures for the issuance and management of permits for permit-required confined spaces
- Providing training for personnel involved in confined space entry, rescue, and air monitoring
- Developing and implementing rescue and emergency response procedures
- Conducting periodic evaluations and audits of the confined space safety program to identify areas for improvement
By implementing a robust confined space safety program, employers can help ensure that workers are protected from the hazards associated with confined spaces and that the workplace complies with OSHA regulations.
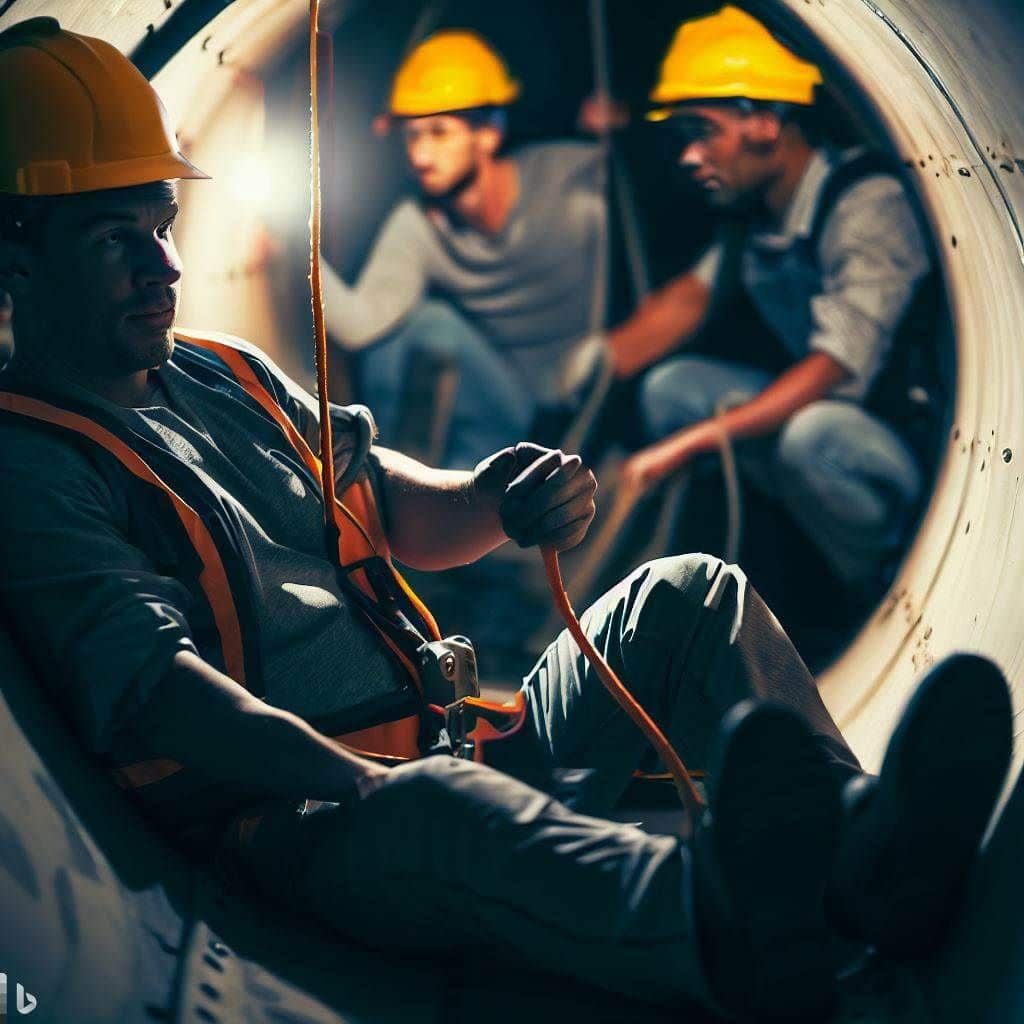
Common Challenges and best practices in confined space air monitoring
Implementing an effective confined space air monitoring program can be challenging. Still, by understanding common challenges and adopting best practices, employers can overcome these obstacles and ensure the safety of workers. Some common challenges and best practices in confined space air monitoring include:
- Ensuring accurate and reliable monitoring results: To obtain accurate and reliable air monitoring results, it is essential to calibrate and maintain monitoring equipment properly and to follow manufacturer recommendations for use. Air monitoring personnel should also be trained in properly using equipment and interpreting results.
- Addressing the limitations of monitoring equipment: All air monitoring equipment has limitations, such as sensor drift, cross-sensitivity, or response times. Employers should be aware of these limitations and mitigate their impact on monitoring results using multiple monitoring devices or incorporating additional safety measures.
- Developing effective alarm procedures: Alarm systems are essential to confined space air monitoring. However, they are only effective if workers understand the procedures to follow in the event of an alarm. Employers should develop clear and concise alarm procedures and ensure that workers are trained in them and understand their responsibilities in the event of an alarm.
- Maintaining documentation: Proper documentation of air monitoring activities and results is important for demonstrating compliance with OSHA regulations and identifying trends and improvement areas. Employers should establish procedures for maintaining records of air monitoring activities, including pre-entry testing, continuous monitoring results, and incidents or corrective actions taken.
By addressing these challenges and implementing best practices, employers can help ensure that their confined space air monitoring program protects workers from hazardous atmospheres and complies with OSHA regulations.
Conclusion
Mastering OSHA confined space air monitoring requirements is critical to ensuring workplace safety and compliance with regulations. By understanding the key aspects of these requirements, identifying and classifying confined spaces, implementing appropriate air monitoring procedures and equipment, and providing personnel training, employers can create a safer work environment and reduce the risk of accidents, injuries, and fatalities.
Frequently Asked Questions:
1. What is the purpose of OSHA confined space air monitoring requirements?
The purpose of OSHA confined space air monitoring requirements is to protect workers from the hazards associated with hazardous atmospheres in confined spaces, such as oxygen deficiency, flammable gases, and toxic air contaminants.
2. What are some common examples of confined spaces?
Some common examples of confined spaces include tanks, silos, vaults, pits, and tunnels.
3. What is the difference between a non-permit-required confined space and a permit-required confined space?
A non-permit-required confined space is a space that meets the definition of a confined space but does not contain or have the potential to contain any hazards. A permit-required confined space is a space that meets the definition of a confined space and contains or has the potential to contain one or more hazards, such as a hazardous atmosphere, engulfment hazard, or entrapment hazard.
4. What types of equipment are used for confined space air monitoring?
Some common types of equipment used for confined space air monitoring include gas detectors, combustible gas indicators, air sampling pumps and tubes, and multi-gas monitors.
5. What training is required for confined space air monitoring personnel?
OSHA regulations require that employers provide training for personnel involved in confined space entry and rescue, including training on air monitoring procedures and equipment. This training should cover topics such as the hazards associated with confined spaces, the principles of air monitoring, proper use and maintenance of monitoring equipment, and the interpretation of monitoring results.