Understanding the Essentials: What 3 Things Make a Confined Space in the Workplace
Introduction to confined spaces in the Workplace
Confined spaces exist in many workplaces and can pose severe risks to employees required to work within them. These spaces are hazardous due to their size and shape and the potential for dangerous atmospheres and other dangers. This article will explore what makes a confined space and examine the hazards, legal requirements, and safety measures required to protect employees working in these environments.
By understanding the essentials of confined spaces, employers can take the necessary steps to ensure a safe working environment for their employees while complying with legal requirements and regulations. Additionally, employees will be better equipped to identify potential confined spaces in their Workplace and take appropriate action to minimize risks and ensure their safety.
Defining a confined space: What are the three criteria?
To establish what three things make a confined space, it is essential first to understand its definition. According to the Occupational Safety and Health Administration (OSHA), a confined space is any space that:
- Is large enough and so configured that an employee can bodily enter and perform assigned work;
- Has limited or restricted means for entry or exit (for example, tanks, vessels, silos, storage bins, hoppers, vaults, and pits are spaces that may have limited means of entry.); and
- It is not designed for continuous employee occupancy.
These three criteria must be met to classify space as confined. It is important to note that not all confined spaces pose the same level of risk, and some may require more stringent safety measures than others. Nevertheless, understanding these criteria can help employers and employees identify potential confined spaces in their Workplace and take appropriate action to ensure safety.
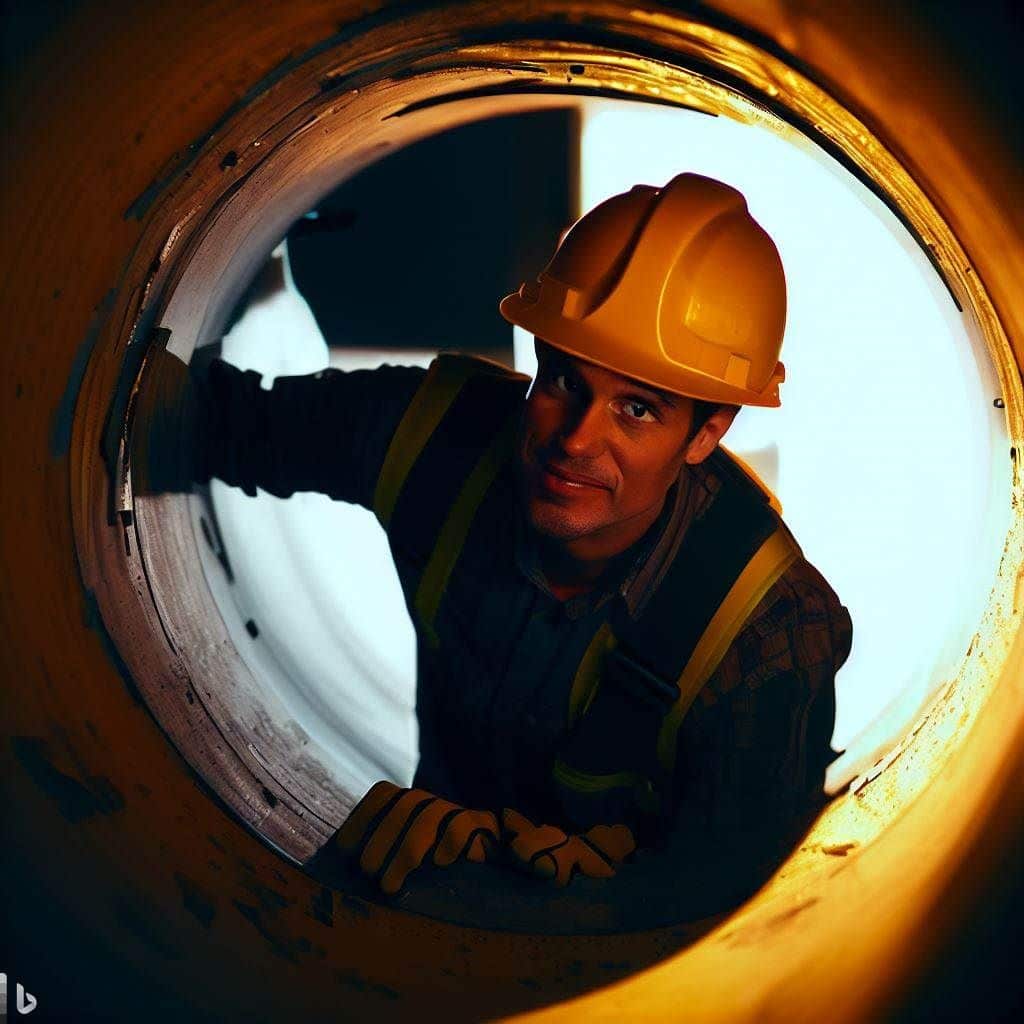
Hazards and risks associated with confined spaces
Confined spaces can present numerous hazards and risks to employees working within them. These hazards can include:
- Atmospheric hazards: Confined spaces may contain hazardous gases, vapors, or particulates that pose health risks to employees. Sometimes, the atmosphere within a confined space may be oxygen-deficient or enriched, posing severe risks.
- Physical hazards: Confined spaces often have limited access and egress, making it difficult for employees to escape in an emergency. Additionally, the space configuration may present risks such as entrapment or engulfment.
- Mechanical hazards: Some confined spaces may contain moving parts or machinery, posing risks to employees if caught or entangled.
- Electrical hazards: Confined spaces may contain electrical equipment or wiring, which can pose risks if they are not properly maintained or if employees are not adequately trained in electrical safety.
It is essential for employers and employees to be aware of these hazards and to take appropriate steps to mitigate the risks associated with working in confined spaces.
Identifying confined spaces in Your Workplace
To ensure the safety of employees working in confined spaces, it is essential first to identify these spaces within your Workplace. Some common examples of confined spaces include:
- Storage tanks
- Sewers and maintenance holes
- Silos
- Tunnels
- Pipelines
- Ducts and vents
However, it is essential to remember that not all confined spaces are apparent or easy to identify. Employers should thoroughly assess their Workplace to identify potential confined spaces and evaluate the associated risks. This assessment should involve input from employees, as they may be aware of areas that management may not have considered.
Legal requirements and regulations for confined spaces
Employers have a legal responsibility to ensure the safety of their employees when working in confined spaces. OSHA has established specific rules for confined space entry and work, which all employers must follow. These regulations include:
- Developing and implementing a written captive space entry program
- Identifying and evaluating all confined spaces within the Workplace
- Ensuring that employees are adequately trained and equipped to work in confined spaces
- Implementing appropriate safety measures, such as ventilation, atmospheric monitoring, and personal protective equipment (PPE)
- Establishing emergency response and rescue procedures
Failure to comply with these regulations can result in significant fines and penalties and an increased risk of injury or fatality for employees working in confined spaces.
Developing a confined space safety program
Employers should develop and implement a comprehensive confined space safety program to ensure compliance with OSHA regulations and protect employees’ safety. This program should include the following elements:
- A written confined space entry policy outlining the procedures and requirements for entering and working in confined spaces
- Identification and evaluation of all confined spaces within the Workplace
- Training and education for employees on the hazards and risks associated with confined spaces, as well as the proper use of PPE and other safety equipment
- Implementation of safety measures, such as ventilation and atmospheric monitoring, to control hazards within confined spaces
- Establishment of emergency response and rescue procedures, including the designation of trained and equipped rescue personnel
By developing and implementing a confined space safety program, employers can help ensure their employees’ safety and minimize the risks associated with working in confined spaces.
Training and education for confined space entry
Proper training and education are essential for employees who work in confined spaces. This training should include classroom instruction and hands-on practice to ensure employees are well-prepared to enter and work in confined spaces safely. Training topics should include:
- Identification and evaluation of confined spaces
- Hazards and risks associated with confined spaces
- Proper use of PPE and other safety equipment
- Atmospheric monitoring and ventilation techniques
- Emergency response and rescue procedures
In addition to initial training, employees should receive regular refresher training to ensure their knowledge and skills remain up-to-date.
Emergency response and rescue planning for confined spaces
In the event of an emergency within a confined space, it is essential to have a well-developed and practiced emergency response and rescue plan in place. This plan should include the following:
- Designation of trained and equipped rescue personnel who are capable of responding to emergencies within confined spaces
- Development of site-specific rescue procedures, considering each confined space’s unique hazards and risks.
- Regular practice and review of rescue procedures to ensure that employees are prepared to respond quickly and effectively in the event of an emergency
By having a comprehensive emergency response and rescue plan in place, employers can help to minimize the risks associated with confined space emergencies and ensure the safety of their employees.
Equipment and tools for working in confined spaces
Employees must have the appropriate tools and equipment to work safely in confined spaces. This may include:
- Personal protective equipment (PPE), such as respirators, gloves, and protective clothing
- Atmospheric monitoring equipment to detect hazardous gases, vapors, or particulates
- Ventilation equipment, to control atmospheric hazards within the confined space- Lighting equipment, to ensure that employees can see and work safely within the confined space
- Communication equipment, to allow for communication between employees working within the confined space and those outside of it
- Rescue and retrieval equipment, such as hoists and harnesses, to assist in the emergency evacuation of employees working in confined spaces
It is essential that all equipment and tools used within confined spaces are properly maintained and regularly inspected to ensure that they are in good working condition.
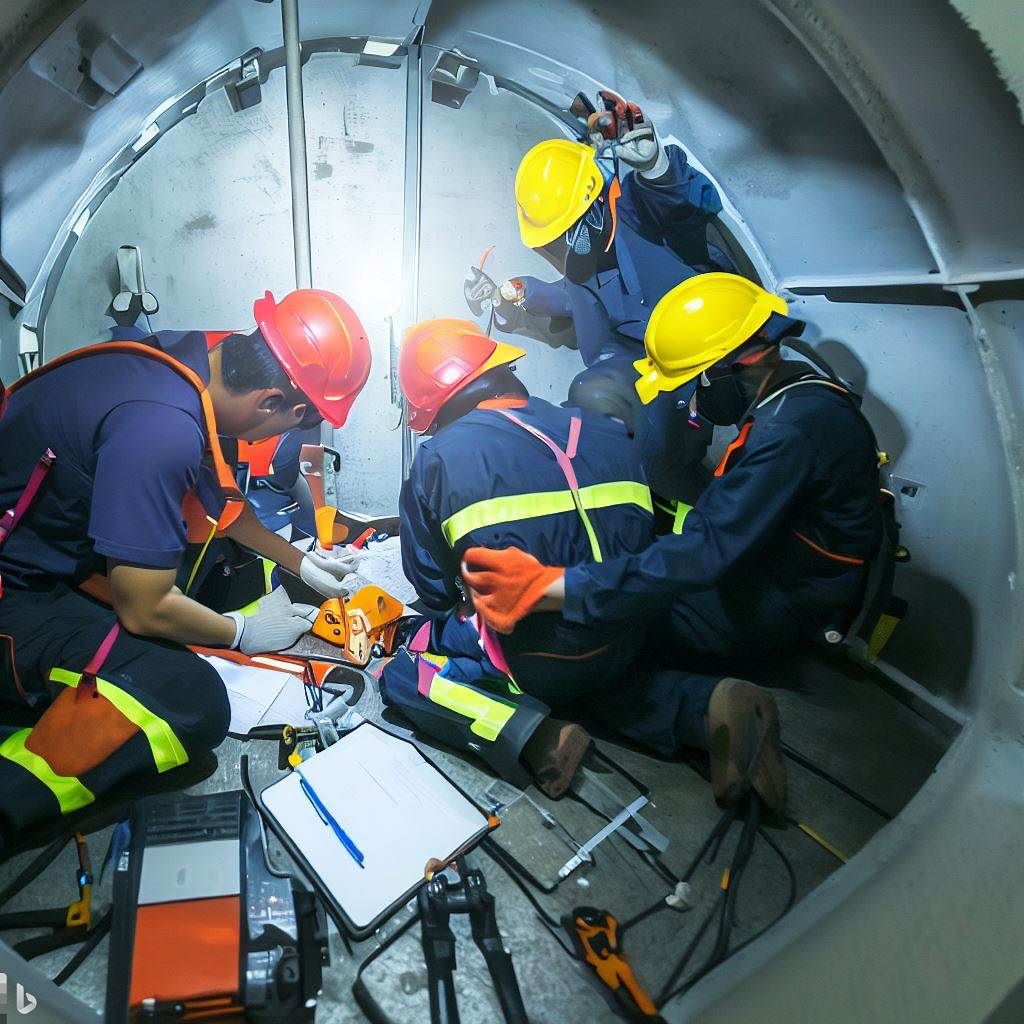
Conclusion and key takeaways
Confined spaces can present severe risks to employees required to work within them. However, employers and employees can take the necessary steps to ensure a safe working environment by understanding the essentials of confined spaces.
This includes identifying and evaluating potential confined spaces within the Workplace, developing and implementing a comprehensive specified space safety program, providing proper employee training and education, and having a well-developed and practiced emergency response and rescue plan.
Key takeaways from this article include:
- A confined space is any ample enough room for an employee to enter and perform work, has limited means of entry or exit, and is not designed for continuous employee occupancy.
- Confined spaces can present numerous hazards and risks, including atmospheric, physical, mechanical, and electrical hazards.
- Employers have a legal responsibility to ensure the safety of their employees when working in confined spaces and must comply with OSHA regulations for confined space entry and work.
- Developing and implementing a comprehensive confined space safety program, providing proper training and education for employees, and having a well-developed emergency response and rescue plan is essential for ensuring the safety of employees working in confined spaces.
Frequently Asked Questions:
Q: What is a confined space?
A: A confined space is any ample enough room for an employee to enter and perform work, has limited means of entry or exit, and is not designed for continuous employee occupancy.
Q: What are the hazards associated with working in confined spaces?
A: Confined spaces can present numerous hazards and risks, including atmospheric, physical, mechanical, and electrical hazards.
Q: What legal requirements must employers comply with for confined space entry and work?
A: Employers must comply with OSHA regulations for confined space entry and work, including developing and implementing a written specified space entry program, identifying and evaluating all enclosed spaces within the Workplace, ensuring that employees are adequately trained and equipped to work in confined spaces, implementing appropriate safety measures, and establishing emergency response and rescue procedures.
Q: What steps can employers take to ensure the safety of employees working in confined spaces?
A: Employers can take several steps to ensure the safety of employees working in confined spaces, including identifying and evaluating potential confined spaces within the Workplace, developing and implementing a comprehensive specified space safety program, providing proper training and education for employees, and having a well-developed and practiced emergency response and rescue plan in place.
Q: What equipment and tools are necessary for working in confined spaces?
A: Equipment and tools necessary for working in confined spaces may include personal protective equipment (PPE), atmospheric monitoring equipment, ventilation equipment, lighting equipment, communication equipment, and rescue and retrieval equipment.